Have you considered how much your compressed air system costs to run? Many business owners haven’t and it’s a common misconception that compressed air is free. It’s only air, right? Wrong
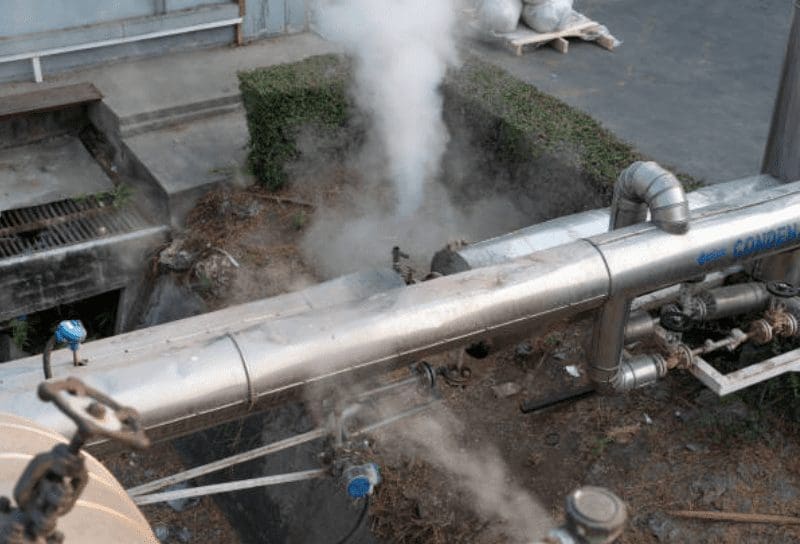
Compressed air is expensive.
Did you know that compressed air is one of the most expensive forms of energy used in industry today?
Often termed the ‘Fourth Utility’, compressed air is just as important to some businesses as electricity, water or gas. It is also very expensive to produce when you consider it takes approximately 7hp of electrical power to produce just 1hp of compressed air power…
10-15% of all industrial electricity is used to general compressed air.
Up to 15% of a plants’ total electricity usage is typically used to produce compressed air. Similarly, the power costs associated with running an air compressor will account for 75-80% of the total cost of owning and operating an air compressor, over a typical 10-year life-cycle.
- Further reading : Compressed air energy management equipment »
- Brochure : Quality and Purity Measurement for Compressed Air and Gases (PDF) »
Typical Compressor System Annual Energy Costs
We reduce your compressed air running costs
At Compressed Air Technology we strive to identify and implement energy saving initiatives to reduce compressed air usage, lower energy costs and reduce carbon footprint.
Our Compressed Air Efficiency Audits can be simple or complex, and are developed in consultation with our clients while evaluating their specific needs. Often, a simple ‘walk the line’ audit can identify opportunities for savings that can be acted upon quickly, easily and at little or sometimes zero cost.
Typical compressor lifetime ownership cost breakdown
For those that wish to take their compressed air system efficiency a step further, we also offer more comprehensive audits, following a five step process to get the most out of your investment and reap the benefits of energy savings hidden in your system…
- Measurement – of the compressed air system, including data logging of power, flow, pressure, dew point and purity over a 7-10 day period to ascertain baseline measurements
- Analysis – of the recorded data and evaluation of the business case for upgrades with simple payback calculations
- Design – of ‘supply’ and ‘demand’ side initiatives to reduce compressed air and power consumption
- Implementation – of identified energy savings initiatives, adhering to proven best practices to ensure payback targets are met
- Verification – of system performance to ensure reductions in compressed air and power usage
At Compressed Air Technology, we do things differently when it comes to auditing, by taking what we call a ‘Systems Approach’. By looking the system as a whole, not just the plant room as is typical, we find opportunities for savings that many auditors may miss. Our ultimate aim is to reduce compressed air usage as much as possible, then match supply with demand to create a truly efficient system
Remember, every dollar wasted on an inefficient compressed air system is a dollar less on your bottom line – do something about it today by booking an obligation free System Assessment…
Further reading : Air compressor leak detection | Compressed air energy management equipment
MORE INFORMATION
Should you require assistance with an existing or new compressed air installation project, get in touch to book an obligation free system assessment.
- Telephone: 1300 663 113
- Email: [email protected]
- Online enquiry form »